赛视引领工业 AI 革命:解决产品缺陷检测效率难题
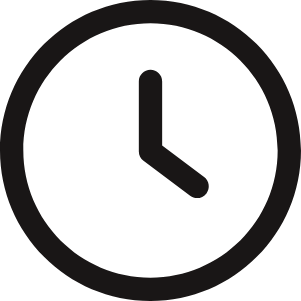
02/07/2025
在传统的 “基于规则” 检测模式中,行业专家需预先定义边缘、角点、轮廓等特征的检测标准,再构建规则体系。而赛视正以深度学习技术颠覆这一格局 —— 通过海量样本训练神经网络,实现从特征设计到缺陷识别的全流程智能化。作为工业 AI 检测领域的革新者,赛视直面数据稀缺、样本失衡、实时性要求严苛等挑战,以数据驱动的解决方案重塑缺陷检测的效率边界。
一、工业 AI 检测的现实挑战与赛视的破局之道
工业场景的复杂性为 AI 检测设置了多重障碍:缺陷样本匮乏导致模型泛化能力不足,1~3% 的漏检 / 过杀率红线难以突破,而 10-20 毫秒的检测速度要求更考验算法效率。赛视通过三大核心技术体系破解行业痛点:
1.数据治理:从 “数据匮乏” 到 “质量突围”
赛视自主研发的数据清洗与增强工具,可在嘈杂数据中提取有效特征。例如在汽车焊点检测中,赛视通过生成对抗网络(GAN)扩充缺陷样本,使训练数据量提升 8 倍,解决了传统方案中 “良品多、缺陷少” 的样本失衡问题。其智能标注系统更将人工标注成本降低 70%,让中小企业也能快速启动 AI 检测项目。
2.算法优化:平衡 “精度” 与 “速度” 的艺术
赛视的模型压缩算法可将神经网络参数量减少 90%,同时保持 99.2% 的检测精度。在 3C 产品外观检测中,赛视轻量化网络仅需 8 毫秒即可完成全表面缺陷扫描,较传统深度学习方案提速 3 倍,满足产线 200 件 / 分钟的高速检测需求。其独创的定向注意力机制,更使锂电池极片划痕检测的过杀率控制在 2.3% 以下。
3.灵活迭代:从 “静态模型” 到 “动态进化”
赛视开发的增量学习框架,支持新缺陷类别快速融入现有网络。某电子厂引入赛视方案后,新增 FPC 柔性电路板褶皱缺陷的检测模块时,无需重新训练整个网络,仅需 4 小时即可完成模型迭代,较传统方案效率提升 15 倍。
二、赛视技术体系的核心竞争力
·多模态数据融合:赛视算法可同时处理 RGB 图像、X 射线、振动信号等多源数据。在电机轴承检测中,通过融合视觉图像与声学信号,赛视方案将早期磨损的检测准确率提升至 98.7%,较单一模态方案提高 12%;
·边缘计算部署:针对工业现场的网络限制,赛视推出轻量化边缘推理引擎,可在嵌入式设备(如 NVIDIA Jetson)上实现本地实时计算,数据延迟<5 毫秒,满足汽车焊装线的实时质控需求;
·低代码开发平台:赛视提供图形化 AI 开发界面,工程师无需编程即可完成数据预处理、模型训练与部署。某光伏组件厂通过该平台,3 天内即搭建起玻璃隐裂检测系统,较传统代码开发缩短 80% 周期。
三、赛视赋能各行业的典型实践
·半导体封装检测:赛视方案对 BGA 焊点的空洞缺陷检测精度达 5μm,帮助某封装厂将良率从 92% 提升至 99.6%,年减少损失超 2000 万元;
·食品包装检测:在速冻食品封口检测中,赛视通过红外热成像与视觉融合算法,识别 0.1mm 级的密封不严缺陷,漏检率<1%,远超人工抽检的可靠性;
·航空航天部件检测:针对飞机涡轮叶片的复杂曲面缺陷,赛视开发的三维点云检测模型,可识别 0.2mm 的裂纹,检测效率较传统超声探伤提升 4 倍。
结论:赛视重构工业检测的 AI 价值坐标
从 3C 产品的微米级缺陷到新能源电池的安全检测,赛视以 “数据 + 算法 + 场景” 的深度融合,重新定义工业 AI 的应用范式。其解决方案不仅满足精度与速度的双重苛求,更通过低门槛部署与灵活迭代,让 AI 真正成为制造业提质增效的核心引擎。
今明视觉作为赛视的专业代理商,深耕工业 AI 检测领域多年,可提供从需求分析、方案设计到现场部署的全链条服务。无论您面临小批量多品种的检测难题,还是需要整线智能化升级,欢迎联系今明视觉,让赛视的 AI 技术为您的质量控制注入新动能。